This roll splicer eliminates the downtime associated with end of roll stops to untended roll fed machines, such as intermittent motion Bartelt pouch filling machines, vertical pouch filling machines, shrink wrappers, etc. The filling or wrapping machine draws the web from the active spindle of the splicer. An operator loads a full roll onto the lower spindle, threads the web to the splice section and stages it in the splice clamp. When the splicer senses an end of roll situation, during the pause of the parent machine, the splicer clamps the web from the new roll against the tail of the web from the near empty roll. The splice is made by a heat seal or a pressure sensitive tape. While the splice is being made a knife traverses the web of the used roll to cut the web. After the cut the splice cycle is complete. The splicer control system interrupts the cycle of the parent machine during the splice cycle to prevent indexing until the splice is complete. After the web has been cut the turret indexes the new roll into the upper position and presents the empty roll to the operator to be replaced with a new one.
Features:
• Up to 40 inch diameter roll capacity
• 3 inch core
• Up to 10 inch wide web
• Thermal or tape splice
• Quick change razor blade knife
• PLC control
• Free standing with leveling pads or caster mount
• Integration with parent machine
• Cantilevered roll spindles
• Optional air shaft
• Adjustable pony brakes
Watch Intermittent Roll Splicer Video
http://www.youtube.com/watch?v=jhbax3eN46I
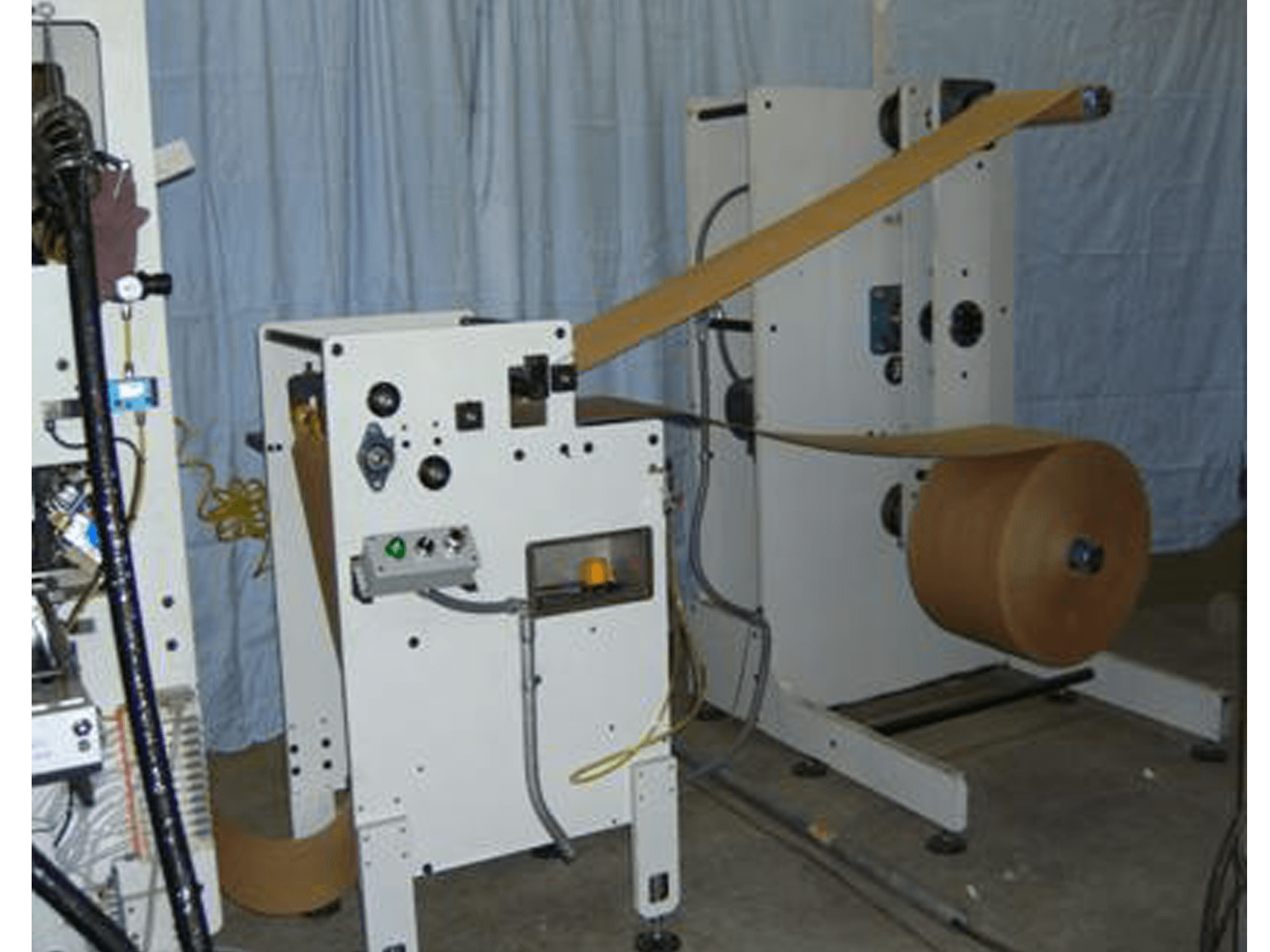